Ceramic membranes filters bring
unique solutions for cleaning of problematic liquid
waste streams.
Based on patented production
processes the membranes have unequalled filtration
characteristics. Pore sizes of the membrane filters
are accurately controlled to allow selective
filtration. Special production techniques result in
an extremely smooth filtration surface which
prevents the build up of fouling. The ceramic
materials and the accurate production processes
result in chemically inert filter tubes that can
also withstand high operating temperatures.Typicall apllications are: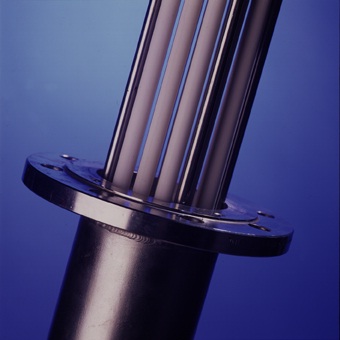
- Oil/water emulsions
- Solvents
- Degreasers
- Thermal heating oil
- PVC dispersions
- Paints
- Brines
The ceramic membrane filter tubes are assembled into PVC or stainless steel modules. The ready
to use modules are available in various dimensions with
filtration surfaces up to 4 m2 per module. Filtration
takes place by dirty fluid passing inside to out of the
membrane tube. The fine porous membrane layer on the
inside of the tube retains concentrated dirty fluid and
the pollutant particles This is called retentate.
Clean fluid passes through to the outside of membrane
tube and is called permeate. On the inside of the
membrane a thin filter cake of is formed. The fluid on
the inside continuously circulates through the ceramic
tubes in cross flow direction to the permeate.
Periodically the fluid flow across the membrane is
reversed in a back pulse. The filter cake on the
inside of the membrane tube is now pushed back into the
retentate stream and discharged.